Product features of the MTR series rack conveyor dishwashers
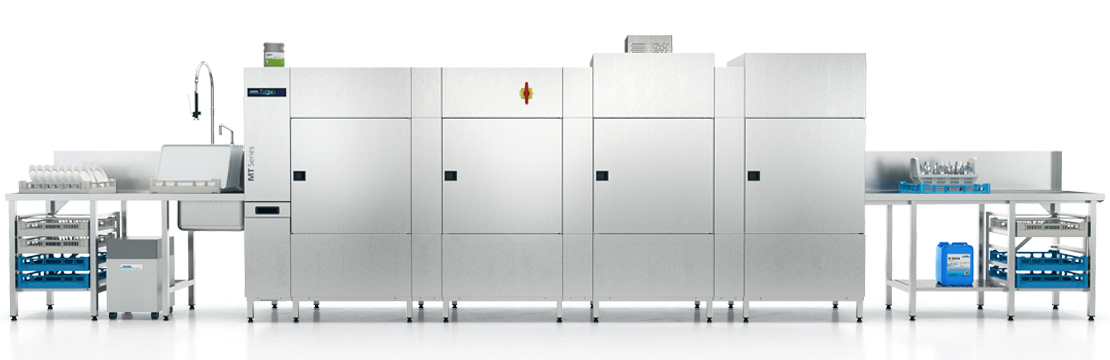
90° corner inlet
The rack drive of the MTR can be extended out of the machine in the inlet and coupled at an angle of 90° with a corner inlet table incl. sink and pre-spray unit. The machine then automatically feeds the racks around the corner. This also reduces the total length of the wash system and allows the MTR to save space when integrated into the room.
Active dirt removal
The MT is also equipped with active dirt removal. It prevents coarse dirt from getting into the tank water in the first place and filters it out before the main wash cycle. The dirt is fed into the inlet zone and collected in the strainer drawer. This can be quickly and easily emptied during operation. This improves the wash result and reduces detergent consumption.
Base installation
An alternative to the standard installation of the MT on feet is the option of mounting the machine on a base. With this variant, the area between the underside of the machine and the feet is closed. This saves cleaning under the machine.
Basic cleaning programme
The MT series has a special programme for basic cleaning of wash items that are soiled with things such as starch: it can be activated when required and relieves the staff of the laborious task of manual basic cleaning. This saves time and costs and makes work easier for personnel.
Blowing-out zone
The air knife drying zone of the MT series is more powerful than the drying zone: it also removes any pooling on the wash items, which improves the drying results. Up to three drying units can be combined.
Built-in solid dosing
The built-in solid dosing SPI (Solid Pump Internal) uses powder detergent. It is highly concentrated and about two thirds more efficient than a liquid detergent. The system is convenient, ergonomic and safe, as the cleaner cartridges can be replaced without any contact with chemicals. Further advantages of the built-in solid dosing include hygienic integration into the machine, space-saving storage of the replacement cartridges and the minimal volume of waste.
CONNECTED WASH
CONNECTED WASH can be used to analyse and evaluate all important machine data from the networked MT and to access it from anywhere. If there is scope for optimisation in the washing process, CONNECTED WASH indicates this with specific recommendations for action, which increases economic efficiency. If a critical errors occurs, the machine automatically sends a notification, ensuring absolute hygiene safety and greater efficiency. Automatic updates ensure that the software on the machine is always up to date and that new functions are available immediately.
Ceiling cleaning jets
For automatic cleaning of the inner ceiling surfaces of the machine, the MT series has special ceiling cleaning jets. These are used to clean the ceilings and rear panels, the top of the warewashing system as well as doors and curtains cyclically with tank water during operation. This reduces the manual cleaning effort and the interior remains permanently hygienically clean.
Container mode
When cleaning containers and other large wash items, the pumped rinse of the MT can be switched off by the operator if necessary. This extends the drip section and improves the wash result.
Continuous rack conveyor
The MTR's drive works with shorter and closely spaced strokes so that the wash racks are transported through the machine at as constant a speed as possible. This provides an almost continuous forward movement and ensures first-class wash results even with dessert bowls and other small hollow bodies.
Corner conveyor
Using an electric corner conveyor, the clean wash items are not transported out of the machine in a straight line, but at an angle of 90° or 180° as required. The racks can also be fed at an angle of 90° in the inlet using the corner conveyor. This enables the space to be used optimally and creates ergonomic workflows. The last drying zone in the MTR series can be installed on the corner conveyor to save space.
Double curtain
The MT is equipped with a double curtain in the machine inlet. As a result, less heat and steam escapes from the machine, reducing energy consumption and improving the room climate.
Double-skinned
The MT series machines have a double-skinned, insulated and fully enclosed stainless steel housing as standard, including base plate and rear panel. This minimises sound emissions and heat losses, allows the machine to be positioned anywhere safely in the room and protects it from water ingress from the outside and damage by rodents.
Drain pumps
The MT series is equipped with drain pumps for emptying the tanks. Unlike simple standpipes, these maintain the water level in the tanks at an optimum level to increase process reliability. Other advantages include an improved wash result, accelerated drainage, a partial drainage option and a high level of occupational safety – as there is only a minimal risk of coming into contact with the wash liquid.
Drying zone
If wash items have poor drying properties due to their shape or material, the drying zone of the MTR helps the thin film of water to dry off. This guarantees optimum drying results – allowing the wash items to be used again quickly.
As an alternative to the straight drying zone, there is also a corner drying zone for the MTR with an angle of 90° or 180°, which can be aligned either to the front or rear of the machine. It is fitted on a corner conveyor and is a space-saving option, as it shortens the total length of the machine and makes optimum use of the space.
Dual detergent saving function
The dual detergent saving function uses an upstream rinse jet at the beginning of the rinse zone to ensure that the majority of the detergent is rinsed directly back into the main wash zone. Furthermore, most of the rinse water is guided around the main wash zone into the pre-wash zone, meaning less detergent needs to be re-dosed. This dual saving measure reduces the consumption of chemicals by up to 80 %, lowering the operating costs of the MT.
Elevated waste water connection
The waste water connection of the MTR is at a height of 300 mm as standard. This prevents the need to penetrate the on-site floor seal for the waste water connection.
Emergency programme
If the MT experiences an error and the machine control no longer functions with the display, an emergency programme can be activated. This prevents a total breakdown of the machine and washing can continue in emergency mode until the service technician arrives.
Error management
While the wash cycle is running, the MT series machines check in the background that all functions are being carried out without error. If an error occurs, a corresponding warning message appears in the display. The MT automatically detects whether the error is self-correctable (e.g. replacement of the detergent), non-critical or critical. For non-critical errors, the machine ensures that washing can continue until the service technician has addressed the issue. Error management reduces possible downtimes and hygiene deficits to a minimum.
Exhaust air adapter
If desired, the MT can be connected to an on-site exhaust air system using the exhaust air adapter. For this purpose, the exhaust air adapter is fitted on the square exhaust air vent of the MT, thus offering the option of being connected to a round exhaust air pipe. The exhaust air adapter can be used with or without heat recovery (not in conjunction with a heat pump).
External energy management
The MT can be integrated into an external energy management system through the interface according to DIN 18875. This makes it possible to cap electrical power peaks, with consideration of all integrated devices, and thereby optimise the total energy costs of the operation.
External liquid dosing
The external liquid dosing PPX (Peristaltic Pump External) is optional, allowing the MT to control the exact dosing of the detergent using a conductance measurement. The efficient interplay between the machine and the dosing device results in even more precise dosing, exploits potential savings and optimises operating costs.
Fast drainage programme
As well as the regular self-cleaning programme, the MT also offers a fast drainage programme: this allows the entire machine to be drained in just a few minutes. This saves time when things need to get done quickly.
FlexSpeed mode
The FlexSpeed mode automatically reduces the transport speed of the MT if it is too high for the current working rhythm. This happens, for example, if the wash items are not cleared quickly enough from the machine outlet causing the washing process to be interrupted. Or, if large gaps occur when loading the machine. Adjusting the speed allows warewashing staff to work continuously. The FlexSpeed mode therefore ensures a smooth workflow and an efficient washing process.
Grease filter for air ventilation
The MT is fitted with two grease filters as standard, which protect the ventilation and heat recovery system from grease build-up. In contrast to machines without filtration, this minimises the amount of cleaning required while maintaining the functionality of the machine and the efficiency of the heat recovery system.
Heat pump
The ClimatePlus heat pump uses not only the thermal energy of the escaping steam but also the energy from the room air to heat the MT's tank and rinse water. The heat pump has a grease filter and an automatic self-cleaning function and reduces energy consumption. This significantly reduces operating costs, the connected load is lowered and the room climate is improved.
Heat recovery
Washing with the MT makes optimum use of the energy input. The "EnergyPlus" heat recovery system uses the energy of the warm air to preheat cold inlet water in addition to the standard "EnergyLight" heat recovery system. Only steam that has already been released is used. This reduces the energy demand of the machine, which lowers the connected load and the operating costs. The heat recovery has both a grease filter and an automatic self-cleaning function.
High temperature washing
If there are special hygiene requirements, it is possible to equip the MT with additional heating power. In HighTemp mode, it is also possible to wash at higher temperatures.
High-performance washing system
The wash arms of the MT's high-performance washing system are arranged asymmetrically for optimum surface coverage when washing. This means that the wash pressure is precisely balanced so that, first, maximum wash performance is achieved and, second, the wash items are held securely in position. The result is a warewashing system that delivers high performance and efficiency – for all types of wash items.
Hygiene certificate
As with all Winterhalter warewashers, the MT series also meets the hygiene requirements of DIN EN 17735 and has the corresponding hygiene certificates. When operated properly, this means that the machines offer full hygiene safety.
You can find more detailed information about DIN EN 17735 in the blog article: "Wash hygiene: the DIN EN 17735 standard".
Hygiene doors
The 180° swivelling hygienic doors give ergonomic access to the entire interior of the machine and allow easy and hygienic cleaning. This is where the big advantages over conventional lifting doors become apparent, because with the high-quality doors on the MT series, the insides are also easily accessible and can be cleaned if necessary. The double-skinned doors are deep-drawn, acoustically and thermally insulated and a central component of the hygiene concept of the MT.
Hygiene mode
Hygiene mode is a product feature only offered by Winterhalter conveyor dishwashers: If the tank or boiler temperature falls below the set value, the MT automatically reduces its transport speed. This ensures full hygiene safety at all times.
Hygiene rear panel
The consistent focus on hygiene can also be seen in the rear panel of the MT. The risers are not installed on the inside of the wash space, but on the outside, so that the surfaces are as smooth as possible. This means that the inside of the hygiene rear panel does not have any areas where dirt could collect. This results in hygienic washing and reduces the amount of manual cleaning required.
Hygiene tanks
The hygienic tanks are another example of the high-quality workmanship of the MT series: They are made of one piece and are deep-drawn in large radii. This means that there are no nooks or crannies in the interior in which dirt can accumulate and deposits can form. Instead, the tanks boast a self-cleaning feature that simplifies and speeds up manual cleaning when needed.
Hygienic tank heater
The MT hygienic tank heaters feature an automatic resettable thermal fuse and have a closed surface. This not only makes them easy to clean, but also increases their service life and reduces service and repair costs.
Integrated hose reel
For manual cleaning of the interior of the machine, the MT series is also available with an optional hose reel. The hose is integrated into a central neutral zone to save space and, with a length of seven metres, is suitable for even the largest possible machine configuration. The practical solution works independently of the MT's water connection, even when the machine is switched off, and saves awkward and time-consuming handling with an extra hose.
Integrated reverse osmosis
The integrated Reverse Osmosis Excellence-i removes up to 98 % of all minerals and salts from the water before washing. Activating the function switches the MT to rinse with osmosis water and delivers wash results of the very highest level: glasses come out of the machine sparkling, cutlery gleams and shines – without the need for polishing. The Excellence-i water treatment system is fully integrated into the machine and does not require any additional space in the kitchen.
Main switch
The MT can be completely disconnected from the mains supply using the main switch if required. This makes it possible to easily, quickly and safely deactivate the machine in dangerous situations or at the end of operation. It also means that the service technician does not have to spend a long time looking for the on-site fuses.
Multi-filtration
The effective multi-filtration system of the MT comprises several strainers, pump inlet filters and Mediamats. The strainers collect the coarse dirt and can be emptied quickly and easily. The pump inlet filter protects the pump from mechanical damage. And the Mediamats remove the smallest particles of dirt from the tank water. The entire filtration system provides first-class wash results and reduces the risk of failure caused by foreign bodies in the system to a minimum.
Multifunction relay
The multifunction relay enables external functions, such as an on-site exhaust air system, to be controlled in relation to the current operational status of the machine. This increases operating safety, improves the wash result and leads to greater energy efficiency in the kitchen, depending on how the multifunction relay is used and the current status of the MT.
Pre-wash zone heat exchanger
Machines in the MTR series with at least three tanks are equipped with EnergyLight heat recovery as standard. The stainless steel heat exchanger uses the hot water from the pre-wash zone to pre-heat cold inlet water. This recovers up to 2.5 kWh/h, which in combination with other features ensures a reduced connected load and savings in operating costs. The heat exchanger also regulates the water temperature in the pre-wash zone and keeps it at the optimum level.
Rack-controlled zone activation
The MT uses water, energy and rinsing chemicals in a targeted and economical manner. The individual zones for pre-wash, main wash and rinse are only activated when there are actually wash items in the respective zone. This conserves resources and minimises operating costs.
Self-cleaning programme
At the end of the day, the MT's self-cleaning programme automatically empties all tanks. During this process, the interior and, if necessary, any heat recovery systems are also rinsed out using rotating jets. This helps the operator with daily cleaning and ensures cleanliness and hygiene.
Separate tank filling
The MT series offers various options for filling and operating the machine. Cold or hot, softened or demineralised water can be used, subject to availability on-site and adjusted to individual requirements. This allows operating costs to be reduced in a targeted manner.
Side wash arms
The main wash zones of the MT series can also be equipped with side wash arms. This ensures that even large wash items such as GN containers or warming trays can be rinsed optimally on their outer sides.
Single tank regeneration
If there is an unusually high level of dirt entering the machine for a temporary period, the water in the first tank can be drained and replaced. The tank water can be regenerated up to 33%, 50% or 100%. As the first tank is refilled using the subsequent tanks, these are also regenerated. This alternative to completely changing the tank water improves the wash results and saves time and money during short production stops, e.g. when changing shifts.
Smart Touch Display
The smart touch display is located on the inlet end of the MT at an optimum working height: with single-button operation, language-neutral interface and self-explanatory pictograms. This makes the machine ergonomic, easy and safe to operate. The glass display is highly robust and sensitive and can be operated reliably even when wearing gloves. During washing, the machine constantly displays the current hygiene status in the form of a traffic light. The current temperatures of each individual zone can also be viewed. These and other functions can be accessed by the operator, chef and service technician on three operating levels.
Speed-dependent rinse water volume
The MT automatically adjusts the rinse water volume to the selected transport speed. At each stage, only as much rinse water is used as is actually required for a first-class wash result. Rinse aid is also dosed dynamically and adjusted to the rinse water volume. This provides for an economical washing process and saves resources.
Start assistant
The SmartStart function checks automatically during filling of the MT that all machine functions are carried out correctly. The start assistant ensures full operating safety and ensures that any errors can be detected and rectified at an early stage.
Strainer detection
The strainer detection system uses a magnetic control to ensure that all strainers are correctly inserted. This is the only way to ensure that the MT's multi-filtration system works optimally and contributes to a first-class wash result. It also optimally protects the pump from damage.
Time-controlled start-up and close-down
With the MT, it is possible to programme at which times the machine should go into or out of operation. The machine then switches on automatically at a certain time, depending on the daily or weekly schedule, and is ready when the first wash is to be done. Or it can automatically start the self-cleaning programme at the end of the day and then switch itself off. This helps to optimise machine operating times, avoid waiting times and save on personnel costs.
Transport speeds
With the MT series, there is a choice of three different transport speeds: "Slow" for heavily soiled wash items, "Medium" for normal soiling and "Fast" for lightly soiled wash items such as trays. The speed values assigned can be adjusted according to individual customer requirements and to comply with the hygiene requirements of DIN EN 17735.
Triple rinse
The powerful triple rinse system of the MT comprises an upstream rinse jet, the pumped rinse and the fresh water rinse. The rinse jet removes dirt particles and detergent from wash items before rinsing. In the process, the used water is fed back into the main wash zone. When combined with the downstream pump and fresh water rinse, the system ensures optimum wash results and minimum operating costs.
USB interface
All operating data for the MT can be accessed through the USB interface and stored externally as a hygiene report. This enables seamless compliance documentation of all hygiene standards according to HACCP. The service technician can also install updates via this interface. This keeps the MT software up to date and newly added functions are immediately available. The USB interface makes this possible even if CONNECTED WASH cannot be used.
Waste water heat exchanger
The MTR with two tanks features the EnergyLight waste water heat recovery system as standard. The stainless steel heat exchanger uses the hot waste water from the machine to pre-heat cold inlet water. This recovers up to 2.5 kWh/h, which in combination with other features ensures a reduced connected load and savings in operating costs.