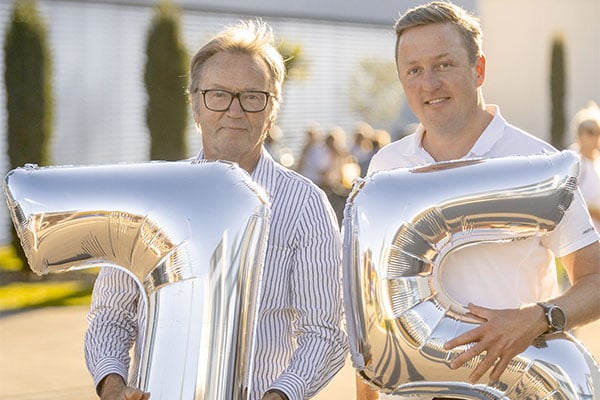
A CLEAN WASH. SYSTEMATICALLY.
High quality standards. That’s what connects us to our customers. We want to deliver more than a warewasher. Our customers come to us because they are looking for a professional solution: tailor-made for their requirements. Reliable and economical. No single product can deliver this. Only a complete system combining a warewasher, water treatment, washing chemicals and accessories can achieve this. Combined with good advice, clear planning and first-class service. Do you share that view?
Welcome to Winterhalter!
THE WINTERHALTER WAREWASHING SYSTEM
WAREWASHERS
For the highest standards of cleanliness and hygiene: commercial warewashers for a wide range of industries. Premium quality and completely reliable.
WATER TREATMENT
For sparkling wash results and effective machine protection: the right water treatment. Integrated into the machine or as an external device.
CHEMICALS
For first-class wash results: detergent and rinse aid for a wide range of applications. Highly effective and economical.
WASH RACKS
For perfect wash results and optimal drying: the right wash racks. Tailor-made for various wash items.
We don’t just sell our customers any warewasher with a host of technical features. We always provide a system for ultra-clean dishes and sparkling glasses.
INDUSTRIES
The catering industry. Bakeries and butcher’s shops. Mass catering and trade. Every industry has its own requirements when it comes to washing. But they all have one thing in common: they want first-class cleaning and maximum hygiene. Winterhalter meets this requirement: with a warewashing system that is designed precisely for the specific industry.
ARE YOU LOOKING FOR SOMETHING SPECIFIC?
Winterhalter has information about all aspects of commercial warewashing. Enter your search term and find the answer.
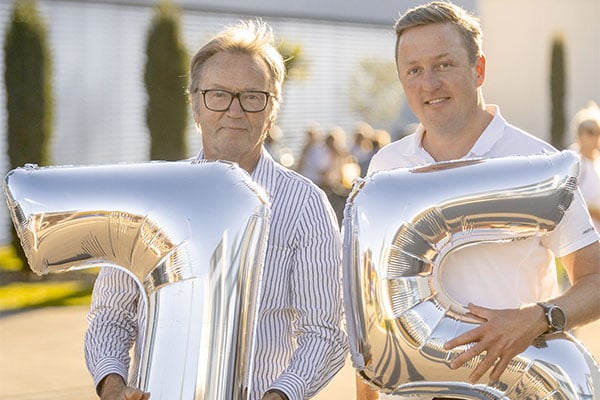